Published on 24 September 2022
Fluid Handling in Microfluidics | Precise Flow Control Solutions
Introduction
Microfluidics is the science of handling fluids in small amounts, inside micrometer-scale channels. On a microfluidic chip, fluids are moved, mixed, or otherwise processed. Such applications use on-chip passive or active flow control techniques, such as capillary forces, micro-pumps, or microvalves. Fluid handling in microfluidics is essential for precise control of liquid movement, ensuring accuracy in lab-on-a-chip experiments, drug delivery systems, and biosensing applications.
But a large number of applications rely on external actuation devices, which include flow control devices to inject and move the fluids, and valves to switch and route the fluids.
Moreover, some measurement methods are often necessary to control flow parameters (i.e. pressure and flow rate). Selecting the best flow control method for your application is very important since the performance and fluid handling efficiency of a microfluidic device depend highly on the flow control system. Flow focusing using a pressure control system… More info
FLOW CHARACTERISTICS AT MICROMETER SCALE
Flow behavior strongly differs at the microscale from its macroscale behavior. Some phenomena, such as gravity, become negligible, while others, such as capillarity, become preponderant.
Some of these new properties are very counter-intuitive. One of the most interesting is characterized by the Reynolds number, which compares the effect of momentum of a fluid to the effect of viscosity. In a microfluidic device, this number is very low. As a consequence, the flow becomes laminar, which means that side-by-side flows are not going to mix. They will exchange molecules only by diffusion. This property is often used in microfluidic devices, to generate concentration gradients, for example.
The drawback is that mixing can be quite difficult. Specific designs (like herringbone or serpentine micromixers) are used when the mixing of several fluids is needed.
FLOW CONTROL SYSTEMS
Flow control is one of the key parameters for microfluidic experiments. Several fluid handling techniques allow us to put fluids inside the chip in motion.
The simplest one is to use hydrostatic pressure. It has the advantage of suppressing external actuation devices. However, the flow stability for long-term experiments is a strong limitation, since the change of level in the inlet and outlet reservoirs causes a change of flow rate. Moreover, this technique is very sensitive to air bubbles.
Then volumetric pumps such as syringe pumps or peristaltic pumps can be used. This technique consists of applying a mechanical movement to modify the volume and create a flow rate. The major drawback of this application is the instability in the flow rate created by the moving mechanical parts of the pump.
Pressure control is also widely used for microfluidic flow actuation. The fluid movement is created by a pressure difference, as defined by the following law: Flow rate = Pressure / Resistance, where the resistance depends on the fluidic path geometry and fluid viscosity.
Other methods, such as electro-osmotic flow or integrated micro pumps are also used for flow actuation in microfluidic devices.
FLOW HANDLING: FLOW PARAMETERS MEASUREMENT
Sensors are often used to precisely know flow parameters, such as the pressure of flow rate, in a specific point of the fluidic path.
Flow rate can be measured with several different techniques: calorimetric, mechanical, acoustic, electro magnetic or optical measurement. To know more about these techniques, please check our dedicated review.
Pressure can also be measured inside the fluidic path, since pressure drops often occur inside microfluid setups. A variety of techniques to measure pressure inside the microfluidic chip have been reported, such as membrane displacement measurement, or air bubbles volume measurement or optical interface tracking. External inline pressure sensors are also available.
[ob1f_rebound]
FLOW HANDLING: FLOW SWITCHING & ROUTING
For microfluidic applications which involve injecting different liquids, a system for flow switching and routing is necessary. This system can be directly integrated into the chip or be external to the chip.
The most famous on chip valves are Quake valves. They involve a bilayer PDMS microfluidic chip. Liquid flows inside the bottom layer, while the upper layer comprises an air network. When activated, the latter can selectively compress and clog channels of the fluidic layer, which allows control the fluid’s motion. Other types of on-chip valves are described in our dedicated short review.
External valves are also often used, and can reduce chip complexity. Among these valves, rotative, 2/2 and 3/2 valves are used. One important requirement in microfluidics is to use low internal volume valves, which are more compatible with microfluidic applications.
References
You will find hereafter a short list of microfluidic publications about fluid handling. If you wish to add a specific publication to this list, please contact us!
- Lee, C. Y., Chang, C. L., Wang, Y. N., & Fu, L. M. (2011). Microfluidic mixing: a review. International journal of molecular sciences, 12(5), 3263-3287.
- Stone, H. A., Stroock, A. D., & Ajdari, A. (2004). Engineering flows in small devices: microfluidics toward a lab-on-a-chip. Annu. Rev. Fluid Mech., 36, 381-411.
- Pittman, J. L., Henry, C. S., & Gilman, S. D. (2003). Experimental studies of electroosmotic flow dynamics in microfabricated devices during current monitoring experiments. Analytical chemistry, 75(3), 361-370.
- Lien, V., & Vollmer, F. (2007). Microfluidic flow rate detection based on integrated optical fiber cantilever. Lab on a Chip, 7(10), 1352-1356.
- Rasmussen, A., Mavriplis, C., Zaghloul, M. E., Mikulchenko, O., & Mayaram, K. (2001). Simulation and optimization of a microfluidic flow sensor. Sensors and Actuators A: Physical, 88(2), 121-132.
- Unger, M. A., Chou, H. P., Thorsen, T., Scherer, A., & Quake, S. R. (2000). Monolithic microfabricated valves and pumps by multilayer soft lithography.Science, 288(5463), 113-116.
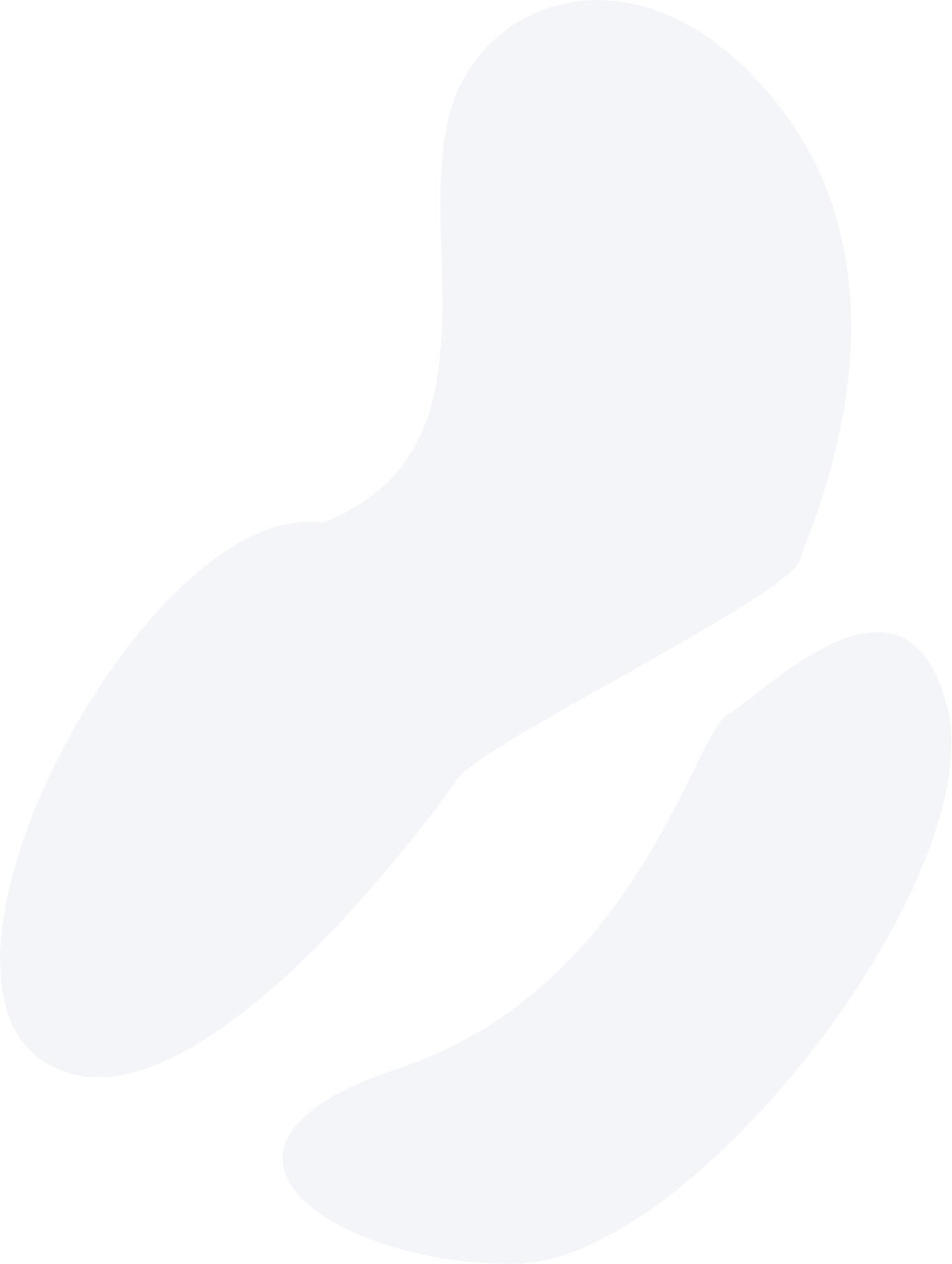
Microfluidics knowledge
Do you want tips on how to best set up your microfluidic experiment? Do you need inspiration or a different angle to take on your specific problem? Well, we probably have an application note just for you, feel free to check them out!